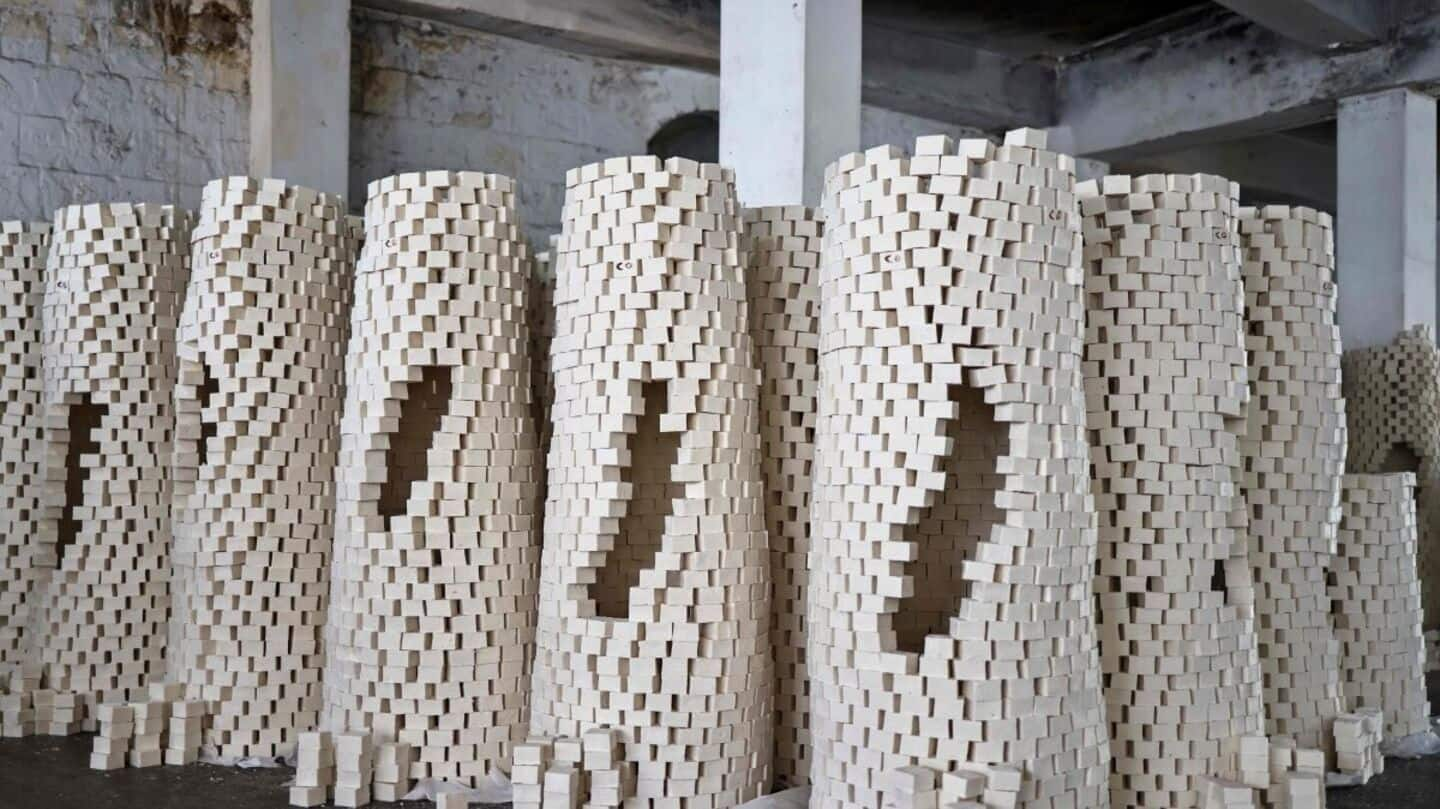
How the Palestinian city of Nablus makes UNESCO-listed soap
What's the story
At the Touqan soap factory in Nablus, workers are continuing a tradition of over 150 years.
At dawn, they start a big furnace to prepare for the day's work: heating a vat of virgin olive oil, water, and lye to make the city's famous olive oil soap.
The tradition was recently recognized by UNESCO as Intangible Cultural Heritage.
Tradition
A legacy of craftsmanship
Musa Assakhal, a veteran soap maker at the factory, carefully checks the mixture's consistency with a metal spatula.
He then activates a large metal blade to stir the thick liquid.
"Once it boils, I'll know whether it's ready or not," he says.
This ancient craft has been handed down through generations in Nablus. Many families produce soap at home.
The Touqan factory is one of the oldest and is still operational today. It opened its doors in 1872.
Difficulties
Challenges faced by the soap factory
Despite its glorious history, the Touqan factory has struggled in recent years.
Growing competition from international brands, along with limitations of Israeli military occupation in the West Bank, has made it difficult to run the business.
These challenges have resulted in cuts to staff and a drop in production by nearly a third.
Israeli military operations in Nablus have added to their woes, with workers finding it harder to reach their jobs or soap shipments to arrive timely.
Recognition
UNESCO recognition amid adversity
Yet, the factory continues to run.
According to Nael Qubbaj, manufacturing manager at Touqan for 30 years, being recognized by UNESCO at such difficult times is especially special.
"In view of this siege, all this political unrest...a UNESCO recognition of our soap brings not only pride, but it is a celebration of many years of working on this soap," he says.
Production
The process of making Nablus soap
The soap-making process at Touqan is multi-stage.
When the mixture is ready, it is carried upstairs in metal buckets, where it's spread out to harden.
Afterwards, porters cut it into bars with long pieces of thread and stack them in cylindrical towers to dry for about three months.
Finally, workers hand-wrap each bar in the company's signature white paper packaging stamped with blue Arabic lettering and two red keys.