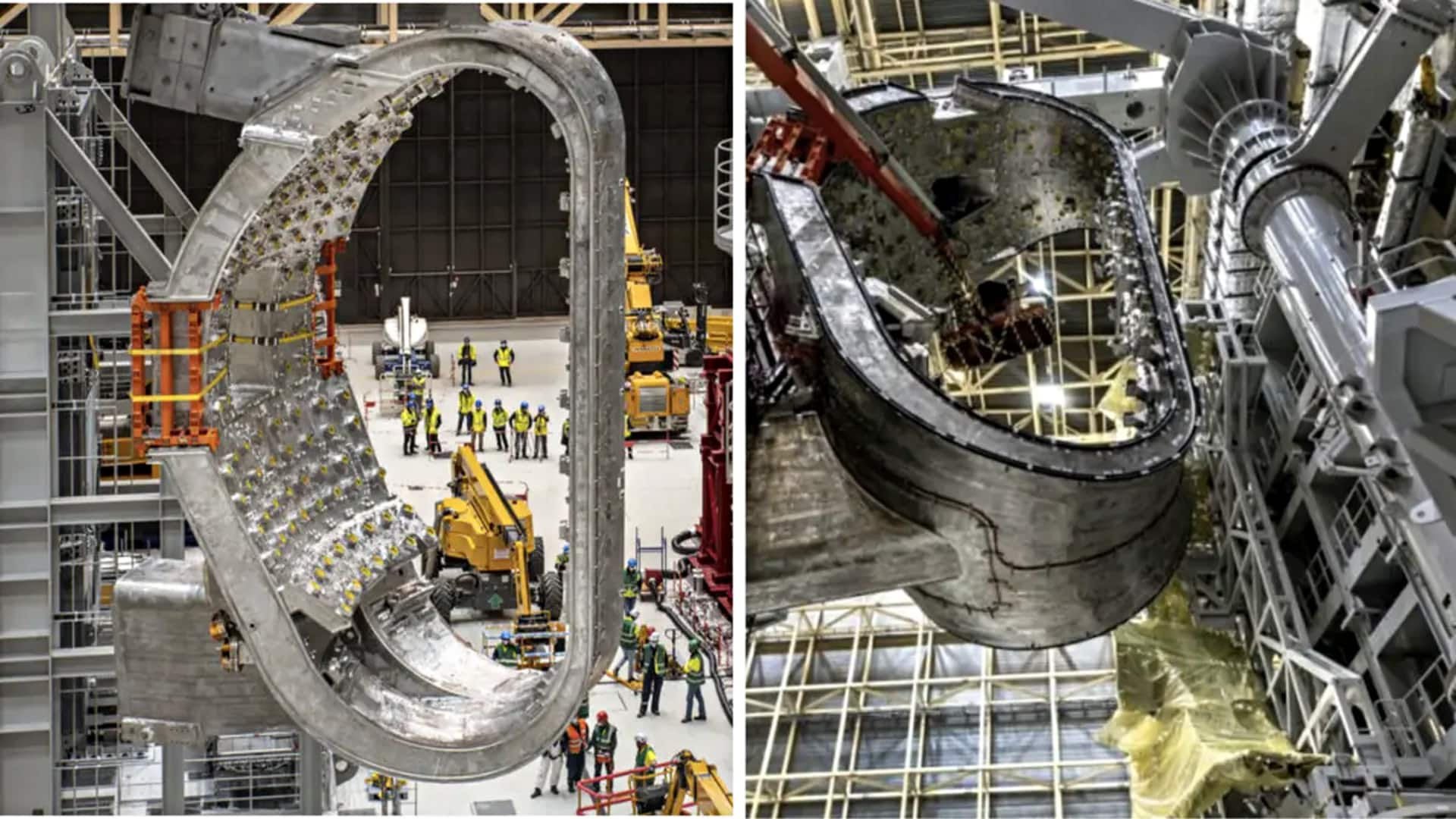
Hyundai delivers final vacuum vessel for world's largest fusion project
What's the story
The International Thermonuclear Experimental Reactor (ITER), which is being built in France, has received its final vacuum vessel sector. The important component was manufactured by Hyundai Heavy Industries at its Ulsan shipyard in South Korea. The vacuum vessel sector will act as the primary confinement barrier for radioactivity, and support in-vessel components like the blanket and the divertor.
Vessel functionality
Vacuum vessel's role in ITER project
The vacuum vessel will house fusion reactions and enable remote handling operations. It will create a high-vacuum environment for the plasma, improving radiation shielding and plasma stability. As ITER explains, the larger the vacuum chamber volume in a tokamak device, the easier it is to confine plasma and reach a high-energy regime that can generate substantial fusion power.
Specifications
A unique experimental arena
With an inside volume of 1,400m3, the ITER vacuum vessel will offer a one-of-a-kind experimental arena for fusion physicists. The double steel walls of the vessel will circulate cooling water to get rid of the heat generated during operation. As many as 44 openings (ports) in the vacuum vessel will provide access for remote handling operations, diagnostics, heating, fueling, and vacuum systems.
Neutron shielding
Vessel's inner surfaces to shield high-energy neutrons
The inner surfaces of the vacuum vessel will be lined with actively cooled blanket modules, shielding from high-energy neutrons produced by fusion reactions. Some of these blanket modules will also be used at later stages to test materials for tritium breeding concepts, according to ITER. This feature further underscores the multifunctional role of the vacuum vessel in the ITER project.
Journey
Journey and construction of the vacuum vessel
The first vacuum vessel sector was manufactured in April 2020 and sent to ITER in August the same year. The last sector began its journey on August 24, 2024, rounding Africa's southern tip Cape of Good Hope before proceeding north to the Strait of Gibraltar and into the Mediterranean. It reached ITER on November 8. The construction process included high-pressure water jet cutting, press forming, heat treatment, machining, welding, drilling, and assembly.