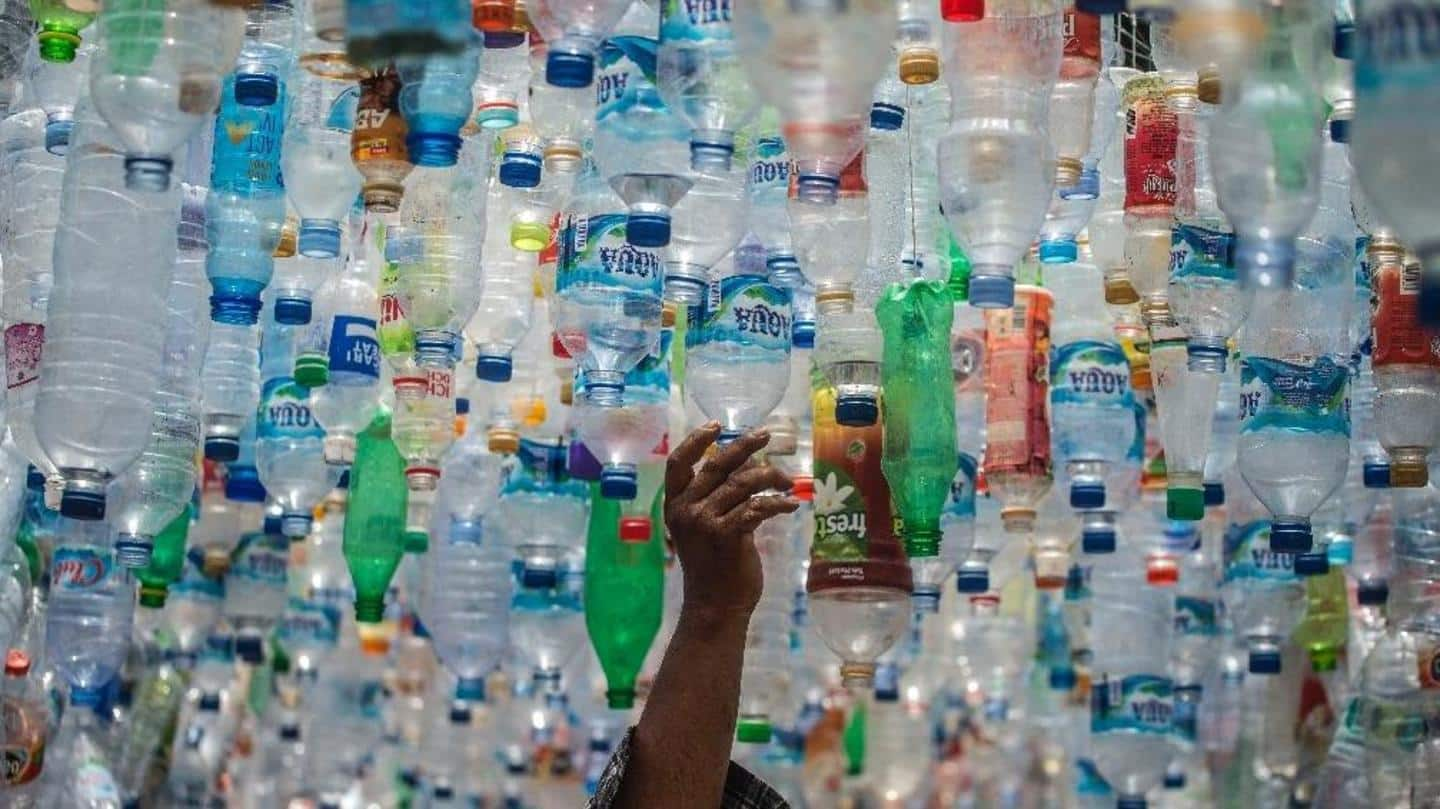
Recycling mixed plastic wastes just got easier; no more separation
What's the story
They say styrofoam cups, food covers, and beverage bottles cannot be recycled together. Well, not anymore. Researchers from Colorado have found a way around it.
In a recent study reported in Science, researchers have formulated a unique two-step process that effectively breaks down mixed plastic waste into useful chemical ingredients by the action of both chemical and biological elements.
Context
Why does this story matter?
There is an undeniable need for plastics in our day-to-day lives. The most prominent use of plastics is as single-use cups, plates, or bottles.
The new research suggests that mixed plastics can be effectively recycled by the combined action of heat and bacteria, resulting in useful products.
However, the pertinent question here is, how marketable are the end products?
Previous research
The research draws inspiration from a 2003 study
The current study draws inspiration from research conducted in 2003 by the chemicals company, DuPont.
The firm worked on heat-based chemical conversion of five major polymers- polyethylene (PE), polyvinyl chloride (PVC), polystyrene (PS), polyethylene terephthalate (PET), and polypropylene (PP). The process involved direct aerobic oxidation with cobalt or manganese-based catalyst.
For instance, PS was successfully converted to benzoic acid with a yield of 88%.
Current study
A biological element is incorporated in the new research
The innovation in the current study is the inclusion of a biological component in the second step after the chemical treatment.
Researchers have employed Pseudomonas putida, a metabolically versatile bacterium that is popularly engineered to utilize various carbon sources.
The microorganisms were allowed to consume oxygenated organic acids resulting from the first step, such as dicarboxylic acids from PE and terephthalic acid from PET.
Result
Chemical products from bacteria were used to make 'biopolymer'
The bacteria made two chemical products, each of which was used to make high-quality performance-enhanced polymers or 'biopolymers.'
During the initial development phase of the conversion process, pure polymer pellets were tested.
Later on, mixed plastics from regularly used products such as single-use PET beverage bottles, styrofoam cups, and HDPE (High-density Polyethylene) milk containers were used for experiments.
Limitations
The scale-up process will depend on economic competitiveness
The major bottleneck of the new technique is the temperature at which the initial auto-oxidation process occurs.
As each type of plastic requires a different temperature, researchers will now work on optimization of the chemical conversion process to improve the yield proportions.
Unfortunately, the demand for the end products resulting from the biological conversion process is smaller compared to the quantity of waste plastics.