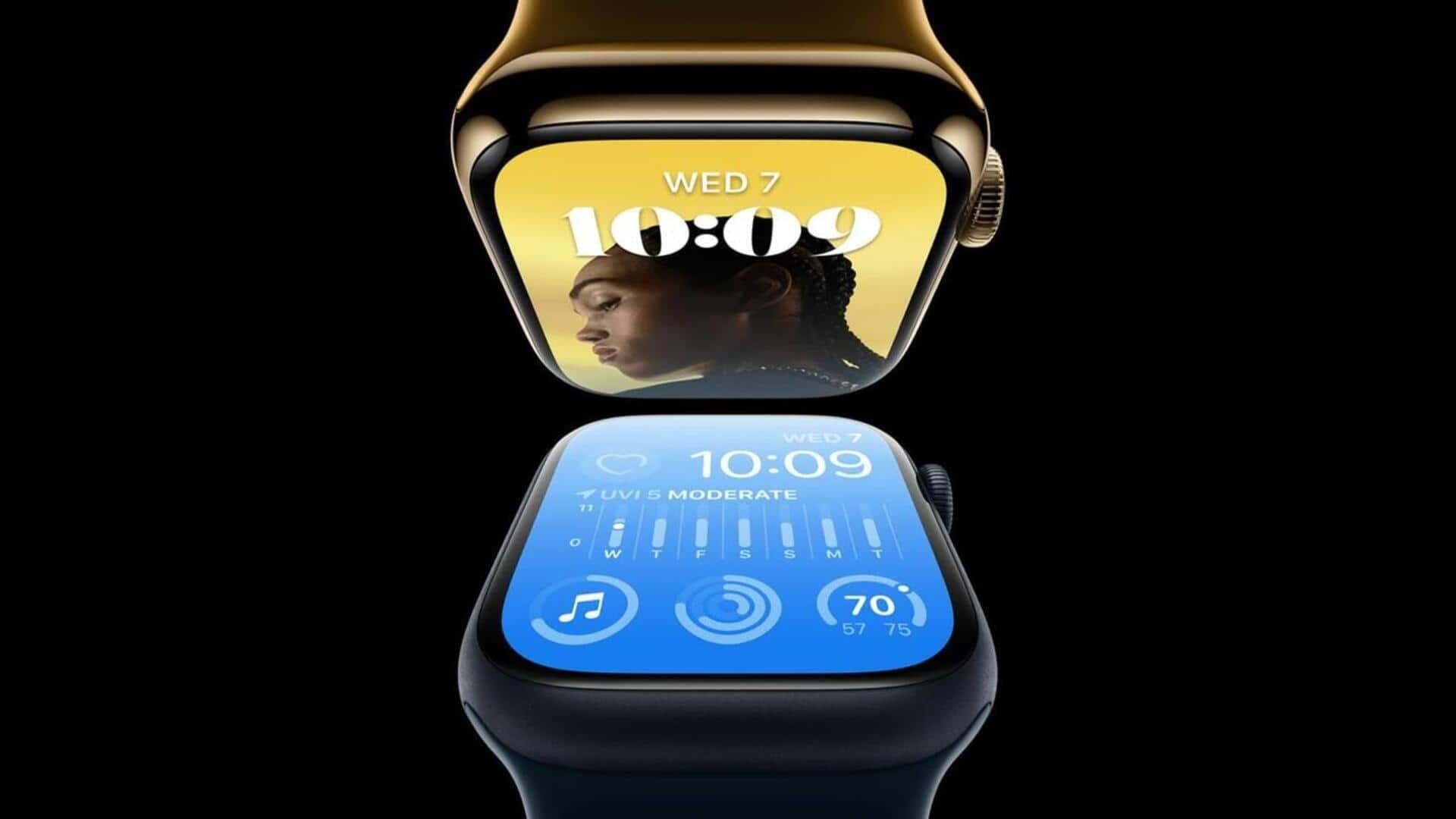
Apple tests using 3D printers for producing smartwatches
What's the story
In a departure from its conventional manufacturing practices, Apple is actively exploring the utilization of 3D printers to craft steel chassis for its upcoming line of smartwatches. This pioneering approach holds the capacity not just to streamline Apple's supply chain but also to catalyze a more extensive transformation within the broader industry.
Details
3D printing may revolutionize Apple's supply chain
Apple's experimentation with 3D printers for steel chassis in its smartwatches could lead to a more efficient supply chain and a wider industry shift. If successful, the tech giant plans to expand this process to additional products over the next several years. The Apple Watch X, said to debut next year, may be the first one to make use of 3D printing technology.
What Next?
Traditional manufacturing vs new technique
Until now, Apple has adhered to a standard manufacturing process for its stainless-steel watches, constituting roughly 10% of the total units in the product line. Forging is used to shape bricks of material into smaller metal blocks, closely resembling the device's size. A CNC machine then carves the metal to create the precise design and button holes. The new technique employs binder jetting, a specific type of 3D printing, to generate the device's general outline at nearly its actual size.
Insights
Binder Jetting: An eco-friendly production technique
Binder jetting involves using powdered material in the printing process, followed by sintering, where heat and pressure are applied to condense the material into a form resembling conventional steel. The exact design and cutouts are then milled, similar to the previous process. This eco-friendly approach minimizes material usage by employing just the necessary metal quantity for the device enclosures.
Facts
Apple's innovation paves the way for transforming tech manufacturing
If Apple's experimentation with 3D-printed smartwatches proves successful, the company plans to expand this process to more products in the coming years. This initiative represents one of the first instances of using the binder jetting method to mass-produce high-volume metal parts. This innovative approach carries the potential to enhance Apple's supply chain and spark a broader shift in the tech industry toward more sustainable and efficient manufacturing processes.