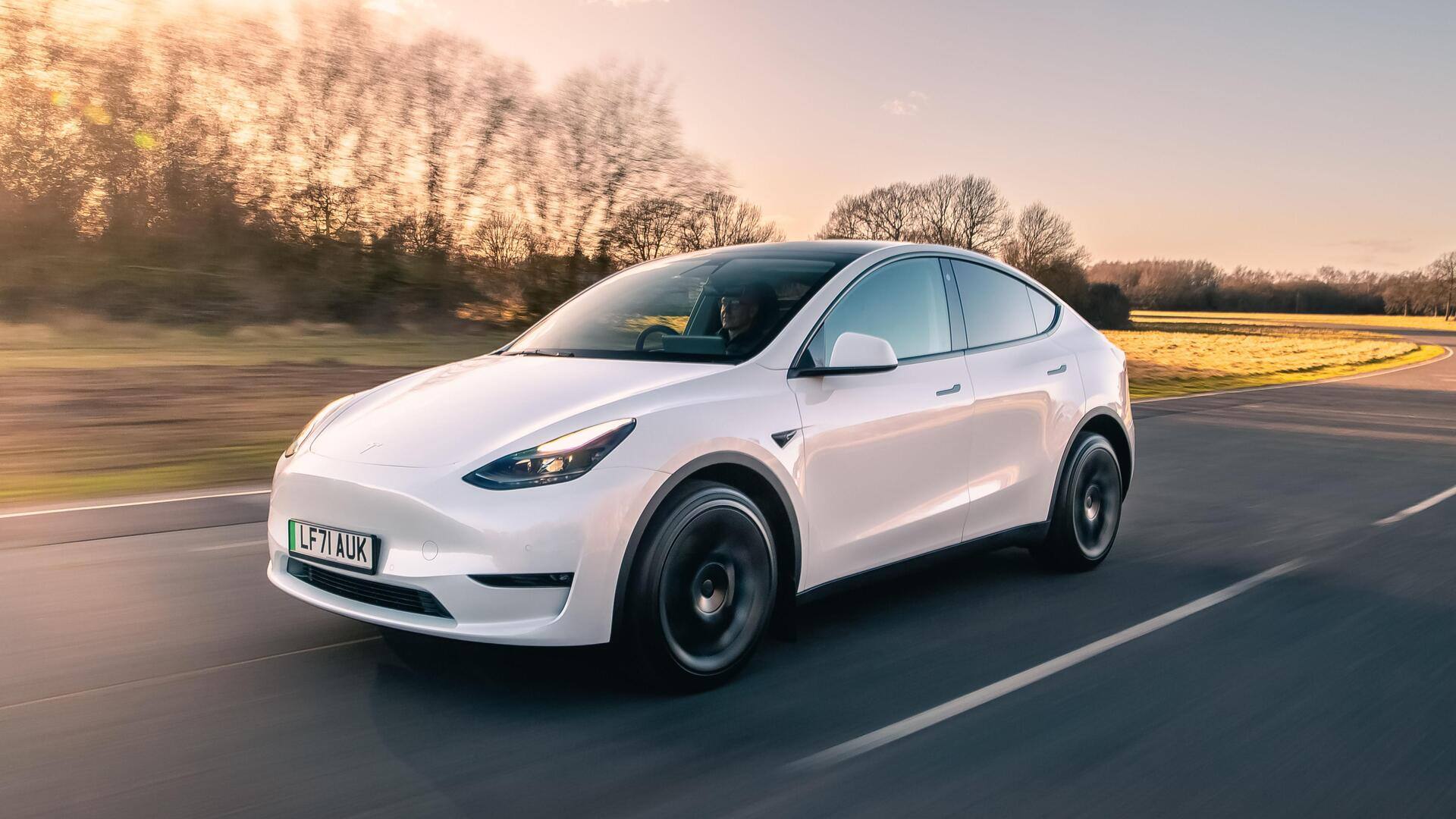
Tesla achieves a breakthrough in making affordable EV manufacturing profitable
What's the story
Tesla is on the verge of a major technological breakthrough that could change the way electric vehicles (EVs) are made, according to Reuters. The innovation involves die-casting nearly the entire complex underbody of an EV in a single piece, as opposed to around 400 components in a conventional car. This development is central to Tesla's "unboxed" manufacturing strategy, which aims to produce tens of millions of affordable EVs in the coming 10 years while maintaining profitability.
Details
Accelerating production with an "unboxed" approach
Tesla's "unboxed" manufacturing approach involves creating large sub-assemblies of a vehicle simultaneously and then snapping them together. Reportedly Tesla's new design and manufacturing procedures could enable the company to develop a car from scratch in 18-24 months, compared to the current industry standard of three to four years. Terry Woychowski, president of US engineering company Caresoft Global, said that if Tesla succeeds in gigacasting most of an EV's underbody, it would further disrupt automotive design and manufacturing.
What Next?
Industrial sand and 3D printing revolutionized casting
The breakthrough Tesla achieved focuses on how giant molds for large parts are tested and designed for mass production, as well as how casts can fill hollow subframes with internal ribs to reduce weight and improve crashworthiness. The innovations, developed by specialists from the UK, Germany, Japan, and the US, involve industrial sand and 3D printing. The cost of the design validation procedure with sand casting is minimal, accounting for just 3% of the cost of using a metal prototype.
Insights
Overcoming challenges with custom alloys and techniques
Tesla's breakthrough in die-casting the EV underbody in one piece involved overcoming several challenges. The aluminum alloys used in the castings worked differently in sand and metal molds, often failing to meet Tesla's conditions for crashworthiness and other attributes. The casting specialists resolved this issue by preparing special alloys, fine-tuning the molten alloy cooling process, and developing an after-production heat treatment.